Mechanically Expanding Tubes with Seal or Strength Welds
Expanding tubes after they have been welded can be frustrating for operators. If not rolled properly, tube material can build up and put stress on the weld. In extreme cases the tube material can build up so much that the expander can get stuck in the tube, delaying the job.
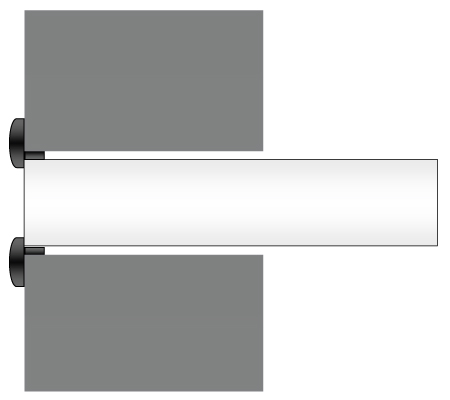
Seal Weld
Seal and strength welds are the two main types of welds used when building exchangers.
Seal welds provide additional leak prevention between the tube and the tube sheet. They are often used to prevent fluids from coming in contact with corrosive materials in the vessel, primarily the tube sheet.
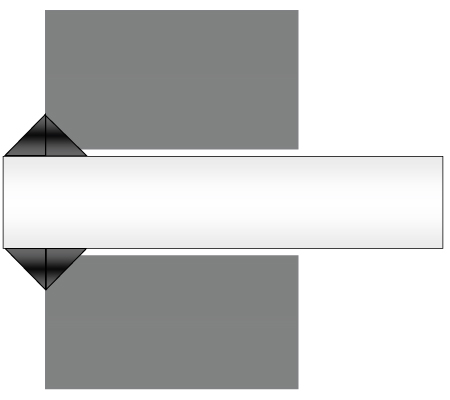
Strength Weld
Strength welds are designed to carry longitudinal tube loads and provide leak tightness. These welds are essentially the same as seal welds, except the tube hole in the tube sheet is grooved. This allows filler metal to be deposited and provide joint strength.
If a tube is strength welded, mechanical expansion is not technically required, since the weld acts as the mechanical joint. However, many customers choose to mechanically expand anyway to prevent crevice corrosion. After a tube is welded, a small gap can be left between the tube OD and the ID of the tube sheet hole. Overtime, corrosion can occur in the gap and cause leaks or weaken the integrity of the joint. Mechanically expanding after strength welding will eliminate any gaps that are present and prevent corrosion.
Expanding Welded Tube Joints
While expanding seal welded tubes can be a challenge, there are a few methods that can make this process easier.
Use Relief Rolls
When tube ends are welded, the amount of heat needed to create the weld causes the material to harden. If the expanding rolls come in contact with the welded bead during expansion, they will break.
In order to prevent the rolls from coming into contact with the weld, a relief can be used. Relief rolls work the same as traditional rolls, however, the back of the roll has a smaller diameter to prevent it from coming into contact with the welded portion of the tube. Relief rolls allow the tube to be expanded normally while preventing premature tool failure.
Adjust Expander Roll Depth
Generally, when setting up an expander the rolls are set slightly back from the tube sheet. This ensures that the tool doesn’t roll beyond the tube sheet. However, in cases where the tube sheet is thicker than the roll length, the expander roll depth can be set past the weld.
In this scenario, an expander with double radius rolls should be used. Double radius refers to the smooth taper that is present on both ends of the roll. This allows for a smooth transition and prevents any ridges or lips from being left inside of the tube after expansion.
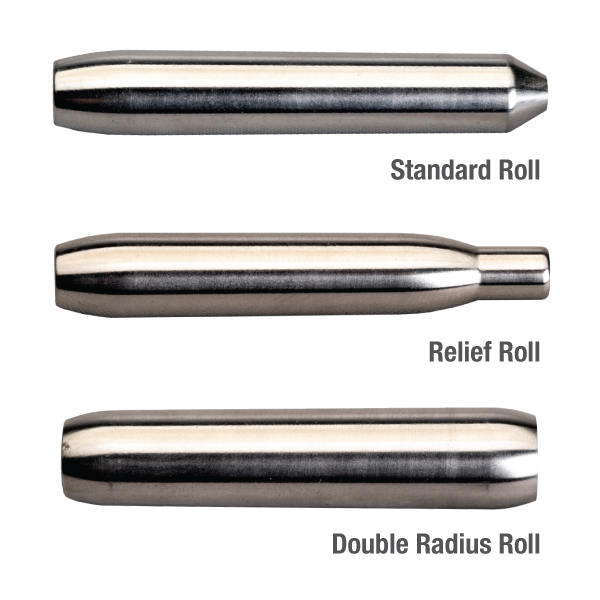
Parallel Pin Expansion
Parallel pin expansion refers to the alignment of the rolls with the mandrel. A traditional expander’s rolls are set at an angle to the mandrel. This feed angle causes a screw-like action that automatically feeds the mandrel into the tube as it rotates. With parallel pin expansion, the rolls are set parallel to the mandrel with zero feed angle. This means that the mandrel will not self-feed as a traditional expander would. Instead, the mandrel is pushed through the expander by force causing the tube to expand.
Some end customers are requiring manufacturers to use parallel pin expansion on seal welded tubes, because they believe this process can better protect the integrity of the weld. In traditional expansion, the feeding of the mandrel introduces a pulling force on the tube, which can create stress at the weld. With parallel pin expansion this force could be reduced or eliminated since the mandrel is being pushed into the tube and the rolls are being forced directly outward towards the tube wall.

Since a parallel pin expander requires force to push and pull the mandrel, this type of expansion is most commonly used with an assisted rolling system. Assisted tube rolling systems are one of the most effective ways to prolong tool life and increase productivity. This is because they’re often equipped with features like a built-in torque control, an expander holder, and an auto-lubrication system. Thus, an assisted tube rolling system would be a good option for businesses that are looking to do more parallel pin rolling.
Overall, expanding tubes after they have been welded can be very frustrating for operators if not done properly. Using relief rolls, rolling past the weld, and parallel pin expansion can make expanding welded tubes easier, while maintaining the integrity of the weld.