Best Practices For Working With Enhanced Tubes
Enhanced surface tubing has grown in popularity in recent years, with many different styles and options available. While enhancements are preferred for efficiency, they can pose some challenges to operators. As a result, it’s important to be aware of best practices before working with enhanced tubes to ensure that the job is done efficiently and without any damage.
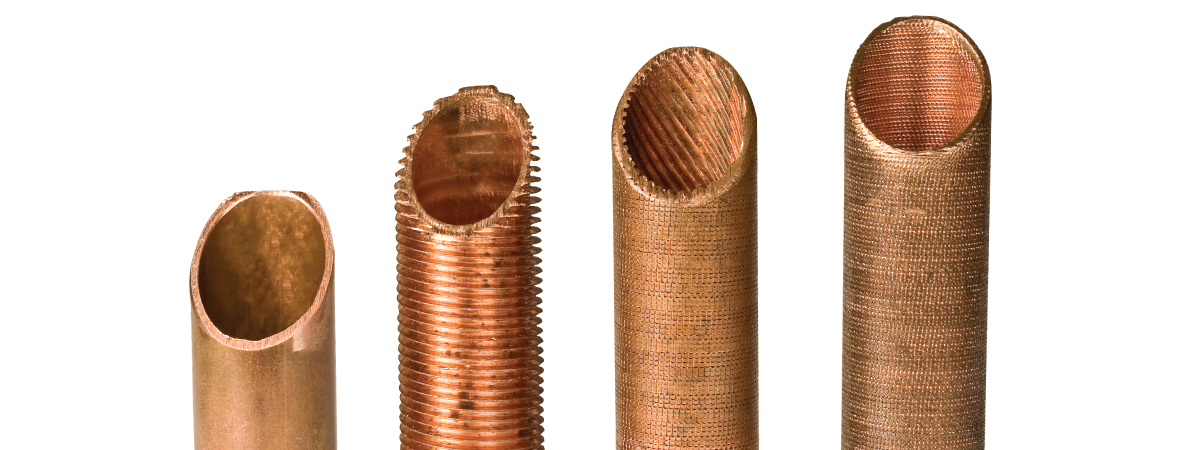
What Are Enhanced Tubes?
An enhancement refers to any type of pattern or form created in the surface of a tube. Tube enhancements are used in both heat exchangers and boilers, varying in size, pattern, and style. Despite the differences in appearance, all tube enhancements have a common purpose: to increase the energy efficiency of a vessel.
Heat Transfer Efficiency
Heat transfer is the flow of energy (heat) from one object to another. The efficiency refers to the actual output of the vessel in comparison to the “ideal” output.
One method for increasing efficiency is through surface area. In general, the more surface area that a substance comes into contact with, the higher the efficiency of heat transfer. This is because there is more area for the medium in (or around) the tube to come in contact with, effectively heating or cooling it down faster. As a result, enhancements are a great way to increase the area for heat transfer, without increasing the size of the vessel.
Types Of Tube Enhancements
There are many different styles of enhancements, with a majority being custom designs to suit a specific vessel. Some of the most common enhanced tube surfaces are internal rifling, micro deformation, and external enhancements.
Internal Rifling & X-ID® Tubes
Internal rifling is a spiral shaped enhancement that is made on the tube ID to create a vortex inside of the tube. This increases surface area and the speed at which a fluid or gas travels through the tube. Rifling can be found in both heat exchanger and boiler tubes.
In boilers, this pattern is often referred to as X-ID® tubes and can be found in many new or newly retubed vessels. While very similar to rifled heat exchanger tubes, X-ID® tubes consist of peaks or ridges that stand up off of the tube ID, as opposed to a recess.
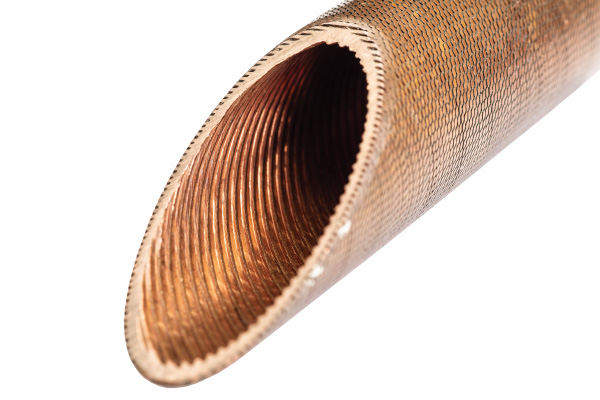
Rifled Heat Exchanger Tube
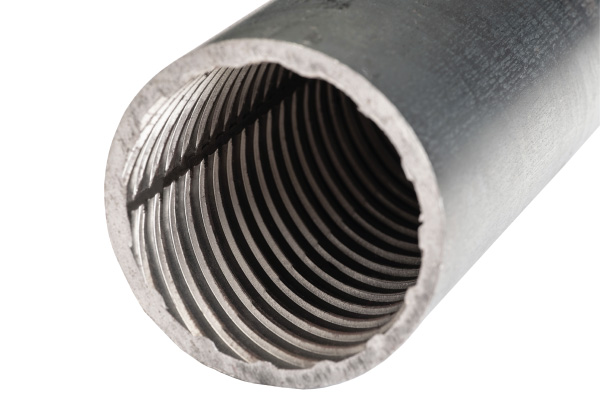
X-ID® Boiler Tube
Micro Deformation
Micro Deformation (MD) tubes consist of a series of small ridges in the tube ID. This pattern increases the surface area of the tube, thus increasing the chiller’s efficiency. The increased efficiency allows for increased tonnage in a smaller chiller.

Micro Deformation Tube
External Enhancements
In addition to internal tube enhancements, external enhancements can also be used to increase efficiency. One of the most common examples is applied fin tubing often used in air coolers. This is when a thin material is wrapped around the outside of a tube to create a finned pattern. In application, these fins increase the amount of material the air can come in contact with, increasing the rate in which the fluid inside of the tube cools down.
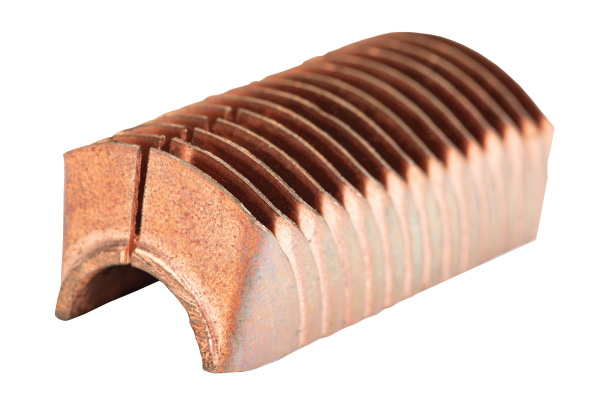
External Finned Tube
Working With Enhanced Tubes
While tube enhancements are beneficial to the efficiency of a vessel, they can pose some unique challenges for tube maintenance. If not handled properly, there is a risk of damaging enhancements and losing efficiency.
Boiler X-ID® Tubes
Tube Installation
X-ID® boiler tubes are one of the most demanding surfaces to expand. This is due to the rifled ID surface being present in the expansion area of the tube.
Best practice when installing X-ID® boiler tubes in a firetube boiler is to select a straight roll tube expander approximately 1/8” (3mm) smaller than the minimum tube ID. Then expand the tube until it creates a metal-to-metal joint with the tube sheet, leaving a 1/8” tube projection. After the tube has been expanded, a roll beading expander sized for a 10 BWG tube can be used as a second operation.
Tube Cleaning
Cleaning X-ID® tubes requires a brush sized approximately 1/8” larger in diameter than the minimum tube ID. This will allow the brush to reach the valleys in the enhancement. Note, the enhancement may also cause the brushes to wear twice as fast, so it’s recommended to have extra on hand.
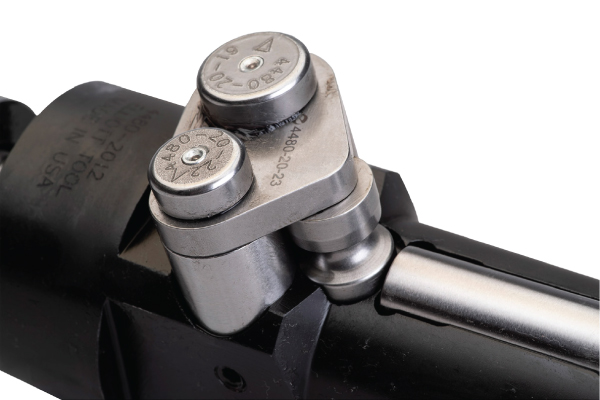
Single Roll Beading Expander
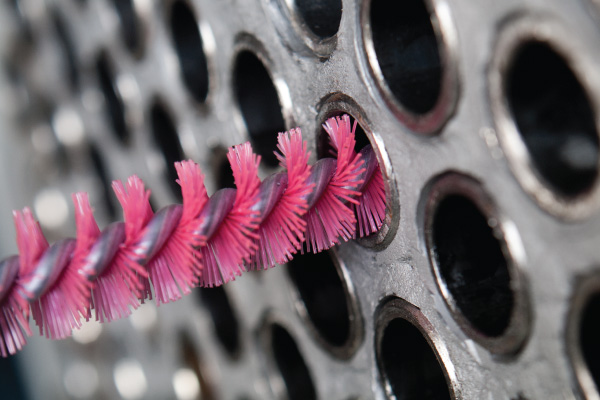
Enhanced Heat Exchanger Tubes
In general, heat exchanger enhancements pose less challenges than boiler tubes when it comes to installation and maintenance. This is because most enhanced tubes have a prime surface at both ends, making it easier to install and perform routine maintenance. However, one area that operators need to be cautious with is tube cleaning.
In order to avoid damaging tube enhancements, it is important that the brush is sized appropriately and that the brush material will not be too rough on the enhanced portion of the tube. In these instances, it is highly recommended that you use a cleaning system or brush designed for cleaning enhanced tubes. When selecting a brush, it’s important to size it to the ID of the unexpanded portion of the tube. If no measuring device is available, several brushes may need to be tested out to find the right size. This is done by inserting and removing each brush from the tube until little to no resistance is felt and the brush rotates through the enhancements.
Overall, enhanced surface tubes have become extremely common in both heat exchangers and boilers as a way to increase heat transfer efficiency. While the results are beneficial to end users, it can pose some additional challenges for maintenance operators. As a result, it is important to be aware of best practices for working with enhanced tubes to help increase tool life and to avoid damaging the enhancements.