Basic Principles Of Tube Expanding
Tube Expanding is the process of reducing a tube wall by compressing the outer diameter (OD) of the tube against a fixed container, such as rolling into tube sheets, drums, ferrules, or flanges. To assure a proper tube joint, the tube wall must be reduced by a predetermined percentage. The following chart can be used to calculate proper wall reduction.
Determining Proper Wall Reduction
Tube Test Number | Sample | 1 | 2 | 3 | 4 | 5 | |
---|---|---|---|---|---|---|---|
A | Tube Sheet Hole Inside Diameter (ID) | 0.757 | |||||
B | Tube Outside Diameter (OD) | 0.750 | |||||
C | Clearance (A – B) | 0.007 | |||||
D | Tube ID | 0.620 | |||||
E | Tube ID When Metal-To-Metal Contact Is Reached (D + C) | 0.627 | |||||
F | Tube ID After Rolling | 0.636 | |||||
G | Wall Reduction (F – E) | 0.009 |
Sample Tube Size 3/4″ x 16 BWG
- Determine the tube sheet hole ID.
- Determine the tube OD.
- Subtract the tube OD from the tube hole ID.
- Using a tube hole gauge, determine the ID of the tube before rolling.
- Add the dimension found in “D” to the clearance “C” between the tube OD and the tube hole to determine the tube’s ID at metal-to-metal contact.
- Roll the tube to what you estimate to be a good tube joint (by feel or an estimated torque setting) and check the ID of the tube with a tube gauge. Take caution not to over roll as it can cause damage.
- Subtract “F” from the rolled diameter to determine the actual amount of expansion (tube wall reduction) on the inside diameter of your tube.
- This can be converted to a % wall reduction by dividing the actual wall thickness (“B – “D”) into the amount of roll as shown in “G”.
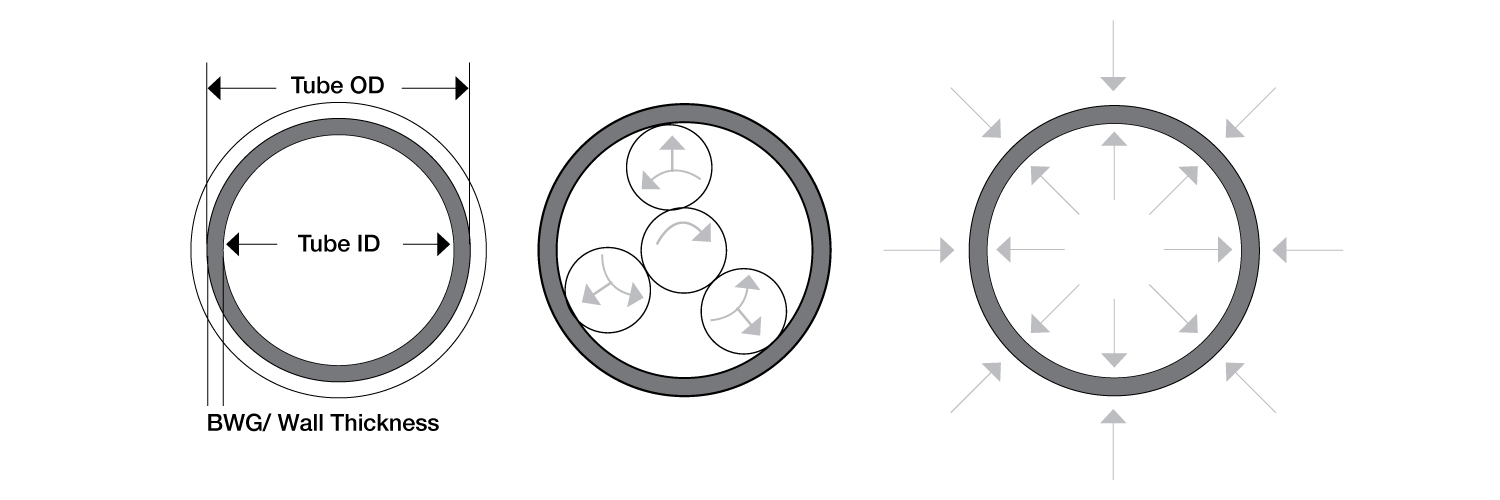
Once metal to metal contact occurs (“E”) any additional increase of the inside diameter of the tube will result in actual wall reduction. Since the amount of wall reduction greatly determines the quality of the tube joint, you should know what percent of wall reduction is optimal for the application.
This technique is an excellent way to set torque rolling devices. Begin with the first sample tube and roll, measure rolled ID, calculate wall reduction, and determine if more or less wall reduction is required. Adjust torque as needed; roll the next tube, etc until proper torque is set. It is better to error on the side of under rolling. Once torque is set these tubes can then be re-rolled to achieve proper tube wall reduction.
Lubrication
Lubrication is critical in rolling a consistently tight tube joint. Tube expanding creates a great deal of heat and friction, so it is important to use the proper lubrication to obtain good tool life and consistent expansions.